D1 - Silver Corrosion Testing and Mitigation
Authors
Jelena LUKIC, Jelena JANKOVIĆ, Dejan KOLARSKI, Draginja MIHAJOVIĆ - Nikola Tesla, Electrical Engineering Institute, Serbia
Sandra GLIŠIĆ, Aleksandar ORLOVIĆ - Faculty of Technology and Metallurgy of the University of Belgrade, Serbia

Summary
Problems of sulphur corrosion in recent years were frequently correlated to the corrosion of silver-plated OLTC. Unfortunately, many cases ended with failure induced by the presence of elemental sulphur (S8), flashover due to flaking of deposited silver sulphide from sliding contacts. Since S8 can’t be natural constituent of refined transformer oils, routes of oil contamination with S8 are important to be recognized. Apart of contamination by oil during regeneration with reactivating adsorbent, other possible ways of oil contamination were recognized, such as: gasket materials, cements, rubbers, reservoirs with used oils and other naphtha residues and fractions, degassing machines, used/contaminated adsorbents. The problem became amplified since the failure investigation records showed that minute concentrations of elemental sulphur in the oil may be enough to trigger failure. This is owing to high ratio of oil mass to the surface of silver-plated contacts that can be affected, especially in designs with in tank OLTC selector. Based on the concentration of elemental sulphur in the oil and data about amount of oil and OLTC in transformer these theoretical values can be calculated. This paper attempts to put more light on this problem, as it became spread even in modern synthetic insulating liquids. High reactivity of elemental sulphur (S8) at low temperatures was observed in laboratory tests and supported by service experiences. It was observed that deposition of silver sulphide can start from low temperatures (room and slightly higher, 40°C if S8 is present in high concentration as of 10-20 ppm). In another case, disulphides, namely dibenzyl disulphide (DBDS) was observed to frequently show suppressed corrosiveness (non-corrosive result) to silver in standardized silver corrosion tests. This is the always the case when DIN 51353 test is performed. Main problem with poor response of DIN 51353 to disulphides is low temperature (100°C) of the test and its short test duration (18h). Another silver corrosion test, ASTM D 1275-15 is performed at higher temperature (150°C) over longer duration (48h) and it has much better response to all reactive sulphur compounds. However, in significant number of tested oils from service, ASTM D 1275-15 was not responsive to the presence of DBDS. It was confirmed in all cases that oils did not contain metal passivator, thus excluding possible interference in the corrosion test by its presence. Another point for consideration in silver corrosion power transformer risk assessment is metal passivator incapability to protect silver surfaces against sulphur corrosion, as shown in previous publications and by service experience. This paper attempts to address these issues, response of DBDS to silver corrosion and metal passivator protective function against silver corrosion. In order to investigate conditions which will promote reaction of DBDS, modification of ASTM D1275-15 test was performed in conditions with oxygen content that showed the increase of DBDS reactivity to silver and is found to be in better correlation to power transformer breathing conditions. Third part of this paper deals with mitigation solutions of oils and transformers contaminated with elemental sulphur. Successful removal of S8 from mineral and synthetic ester oil was performed with success, using innovative technology. Mineral oil contaminated with high concentration of elemental sulphur was successfully treated on lab scale, including large scale oil treatment on distribution power transformer. Further on, trials of the technology on alternative liquids included treatment of synthetic ester oil contaminated with elemental sulphur on lab scale. Promising results were obtained to continue further development.
Keywords
DBDS, elemental sulphur, OLTC, oil treatment, silver corrosion, mineral oil, synthetic ester1. Introduction
The presence of corrosive sulphur in power transformers' insulating fluid still presents severe problems, causing failures during the operation of power transformers. The failure mode related to silver corrosion is more difficult to manage than copper corrosion and this is affecting essentially on load tap changers with their silver-plated contacts [1]. Most of the reported failures occurred after oil regeneration processes with reactivating adsorbents. This working mode causes creation of elemental sulphur during reactivation of adsorbent at high temperatures (from 300°C to above 600 °C) and subsequent contamination of the oil in following oil circulations after reactivation of adsorbent [2]-[8]. However, recent failure cases have been reported that are not directly correlated to oil regeneration involving reactivating adsorbents [2]. Alternative sources of oil contamination with sulphur are coming from the following non-insulating materials: rubbers, cements, gaskets materials, damping materials, water-based glues, incompatible hoses, etc. [3]. The impact of these materials needs to be further studied and assess the compatibility with copper and silver in terms of corrosion of mentioned construction metals. From the perspective of a transformer operator, the failure mode linked to silver corrosion presents multiple challenges. Firstly, a very wide variety of scenarios stemming from corrosive sulfur can lead to failures.
Observations from the field identified two possible failure modes due to silver corrosion: dielectric flashover and thermal hotspot. Flashover is initiated by detachment of silver sulphide particles from the contacts, most often after a tap-changer, operation due to the sliding on the contacts. When silver sulphide flakes detach from the surface of the contact, they become free to move into dielectric-stressed areas. As silver sulphide is rather conductive, these flakes can create a weak insulation path, which can lead to a sudden flashover [3]. If sulphide deposits are growing and remaining on the contacts, they may cause rise of resistances and overheating of the contacts. Conventional detection methods, such as Dissolved Gas Analysis (DGA) and winding resistance measurements, often fail to identify these imminent failures, which can result in unexpected flashovers without any preceding signs. While the annual count of reported instances has remained consistent in recent years, there has been a noticeable shift in the root causes, particularly concerning the nature and origin of the corrosive sulfur.
Elemental sulphur is the most reactive sulphur compound and based on the service experiences it is more reactive to silver than to copper. It can be formed in the reaction of other sulphur compounds (disulphides, monosulphides, etc.) [4]. The risk of power transformer failure becomes amplified due to high reactivity of elemental sulphur to silver and low concentration needed to create silver sulphide. This is due to high ration of oil mass to the surface of silver-plated contact in the cases of in tank selector part.
If present in high concentrations, elemental sulphur can deposit silver sulphide even at normal operating temperatures in short time. Kinetic parameters (reaction rate and activation energy) of silver sulphide formation from elemental sulphur dissolved in the oil on the silver surface are presented in this paper.
Methods for assessment of oil corrosiveness to silver are not adequately responding to the conditions of power transformers in service, nor they are reflecting reactivity of different sulphur species. In practice corrosive sulphur tests were shown to provide different results, depending on the type of sulphur compounds in the oil and their reactivity to copper and silver. This observation was made during practical oil testing and on-site inspections [2]. DIN 51353 test was found to be irresponsive to all reactive sulphur compounds except elemental sulphur, while ASTM D 1275-15 is found to have good response to all other types of reactive sulphur compounds. Nevertheless, significant number of inhibited oils containing DBDS were not responsive to ASTM D 1275-15 and oils were not containing metal passivator. New method is proposed with the attempt to improve the test to better respond to the application of oil in transformers and adequately assess oil corrosiveness. Setting up appropriate tests to determine oil and power transformer condition as well as mitigation solutions are becoming very important nowadays, since problems and failures caused by silver corrosion have increasing trend. Removal of reactive sulphur compounds, by oil treatment is viable mitigation solution. Results of efficient elemental sulphur removal from mineral oils on laboratory and large scale are presented.
2. Kinetics of silver sulphide formation - Reaction of elemental sulphur and silver
Failures of power transformers showed that minute concentrations of elemental sulphur in the oil may be enough to trigger failure. This is owing to high ratio of oil mass to the surface of silver-plated contacts that can be affected by reactive sulphur, especially in designs with in tank OLTC selector. If the mechanism of the reaction is known, these minimal theoretical concentrations of elemental sulphur can be calculated.
It was observed in practice that deposition of silver sulphide occurs at normal operating temperatures [2,3]. Even at 25℃ silver sulphide deposits started to appear, while at 40℃ they became quite significant after only 18 hours (Figure 1).
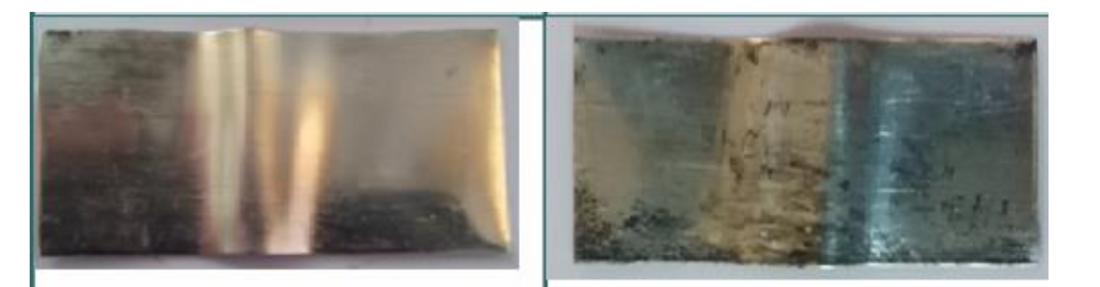
Figure 1 - Mineral insulating oil containing 10 ppm of S8, after 18 hours at 25°C - left and 40°C- right
Proposed mechanism of the reaction of silver sulphide formation is involving the solid-state reaction of elemental sulphur (S8) and silver on the surface of silver, presuming that no metal side reactions occur, such as reduction of elemental sulphur by oil hydrocarbons producing H2S and methane. This is taken as valid, since the above-mentioned reaction are very slow and require higher temperatures, above 200°C [5,6]. Nevertheless, methane concentration was measured at all temperatures to check whether there is an increase of methane concentration above those of neat oil without elemental sulphur. Concentration of 50 ppm was taken as threshold value and safety margin (limit of stray gassing test indicated in IEC 60296) to exclude side reactions due to reduction of elemental sulphur.
At all investigated temperatures (120-140-150-165-180°C) measured methane concentrations were below 50 ppm, going from lowest to highest temperature, respectively, (1 ppm (144.5 h), 1 ppm (108 h), 7 ppm (108 h), 6 ppm (28 h). The exception was 52 ppm of methane measured at highest temperature of 180°C after 65 h, but this small difference within measurement repeatability variance was considered as not important to exclude other side reactions from the proposed silver sulphide formation mechanism.
2.1. Experimental procedure
Mineral insulating oil was spiked with elemental sulphur to achieve concentration of 5.4 ppm. Aging was performed using ASTM D127515 set up at five temperatures: 120℃, 140℃, 150℃, 165℃ and 180℃ in different durations that were adapted to the temperature and expected rate of reaction to achieve ≥ 80% conversion rate. At high temperatures, sampling intervals where on 15 min. -30 min, during one to two days, while at lower temperatures sampling intervals were in several to 12 hours until 6 days of ageing.
Elemental sulphur concentration in the oil was performed using IEC TR 62697-Part 3. Method is based on gas chromatography with EC detector (limit if detection LOD=0.07 mg/kg), the same analytical techniques which is used for DBDS measurement (IEC 62697-Part 1).
Overall mechanism of silver sulphide formation include three steps: diffusion of the sulphur in the oil to the silver surface, adsorption of sulphur on the silver surface and silver sulphide oil interface and diffusion of silver in the silver sulphide layer. First order rate of the reaction is proposed and experimental data were found to fit well to the proposed kinetics:
(1)
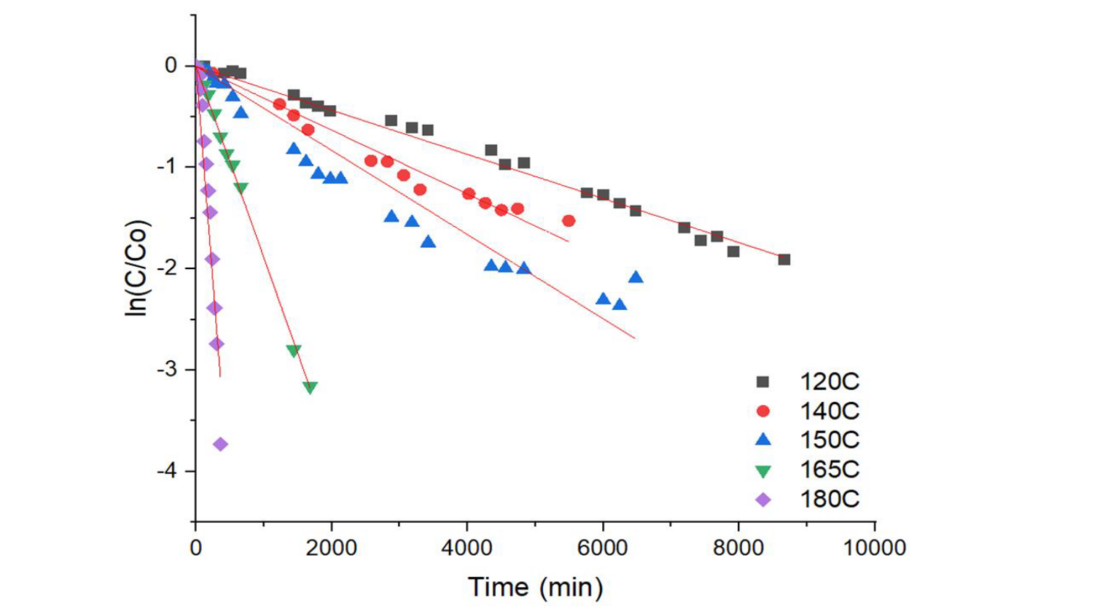
Figure 2 - First order reaction rate fitting to experimental data of elemental sulphur reaction with silver surface at different temperatures
T, °C | k, l/min | lnk | 1/T, K |
---|---|---|---|
120 | 2.18E-04 | -8.4322 | 0.002545 |
140 | 3.16E-04 | -8.06079 | 0.002421 |
150 | 4.16E-04 | -7.78561 | 0.002364 |
165 | 1.89E-03 | -6.27118 | 0.002283 |
180 | 8.53E-03 | -4.76417 | 0.002208 |
It is apparent from the change of the slope that change of the mechanism occurs at 150 ℃ (Figure 3, left).
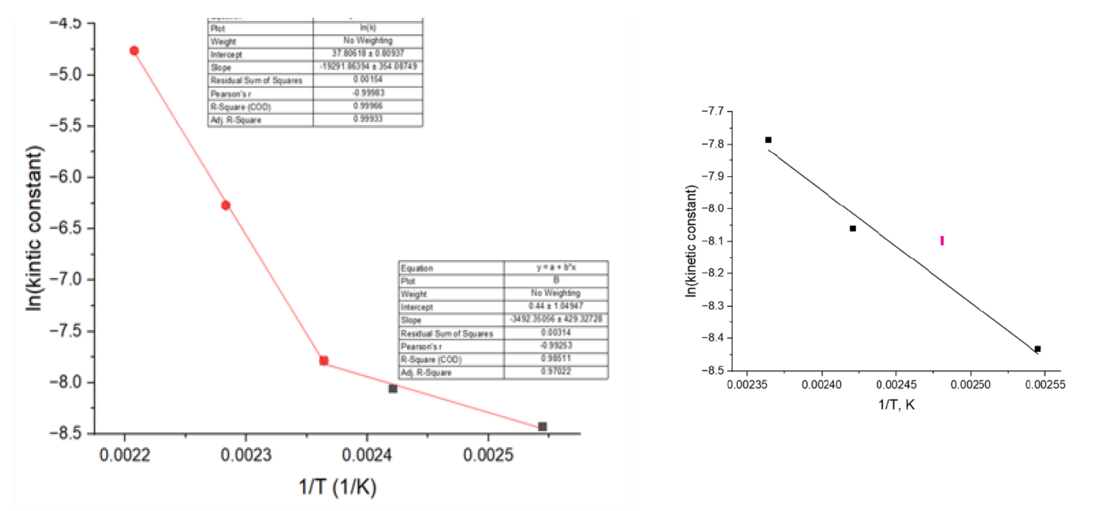
Figure 3 - Kinetic constant versus temperature in the range from 120-140-150-165-180°C - left and in the range 120-140-150°C - right
Lower temperature range from 120℃ to 150℃ was used to calculate activation energy, since these temperatures are admissible hot metal surface temperatures in transformer loading guide IEC 60076-7 and they are in correspondence to the temperatures of corrosion tests applied (Figure 3, right).
Activation energy of 29.04 kJ/mol was obtained for the temperature interval 120-150 ℃, using Arrhenius equation:
(2)
as the slope of the curve (Figure 3-right). Investigation in the future will be performed at temperatures below the 120 ℃ in order to get insight into mechanism of the reaction in broader temperature range with more experimental points.
3. Silver corrosion tests
Different silver corrosion tests available nowadays show different results that may adversely impact transformer condition assessment and risk mitigation. ASTM D1275-15 silver corrosion test is broadly applied, since it responds to the presence of broader range of reactive sulphur compounds in the oil. However, significant numbers of inhibited oils containing DBDS are not responding as corrosive to silver according to ASTM D 1275-15 silver strip corrosion test. This is not in correlation to service experiences and can cause lot of problems in risk mitigation of power transformers, even if the oil was tested for paper wrapped copper corrosion test (IEC 62535) and DBDS content, as proposed in IEC 60422, guide for maintenance of mineral insulating oils in service. The outcome of this scenario is inappropriate mitigation action recommended, based on the wrong understanding that the oil is corrosive only to copper. Decision to apply metal passivator addition would not be effective, since silver is affected by sulphur corrosion and it is not protected by metal passivator addition. Exactly this scenario occurred in real life, power transformer in transmission with oil containing 150 ppm of DBDS failed after addition of metal passivator due to silver sulphide deposition [7]. The main problem in the case example is the poor sensitivity of the method to detect silver corrosion of oils containing DBDS.
In order to address this problem and enable adequate tools for risk assessment, modification of test method to assess silver corrosion is necessary to replicate more closely conditions in transformer and presence of DBDS and other reactive sulphur compounds in the oil.Modified ASTM D 1275-15 silver corrosion test was performed on the oil from free-breathing power transformer in service (10,5 kV, 10 MVA).
Glass bottles (250 ml) with GL 45 screw caps were used, equipped with PTFE coated silicone seals and with a temperature resistance up to 200 °C. Three holes were made, needles were punched into the screw caps, allowing the samples to breathe continuously during the test and providing similar conditions to a free-breathing system of a power transformer (Fig.4 - right). The 220 ml of oil was thermally aged at 150°C in air circulating oven, for 48 and 144 hours. For comparison, standard ASTM D 1275 - 15 was performed (Figure 4 – left).
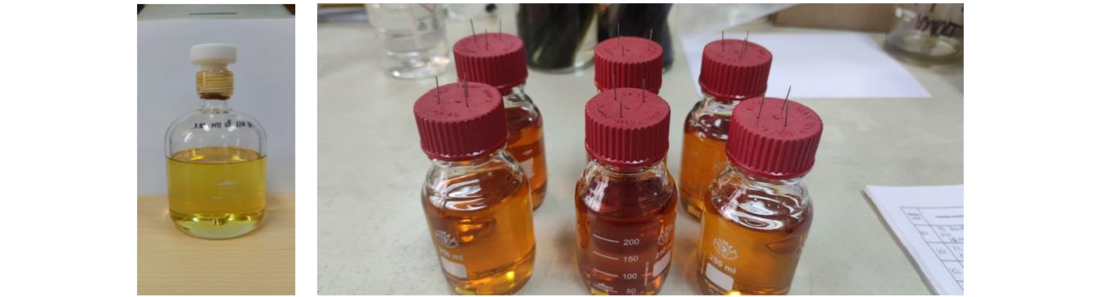
Figure 4 - Standard ASTM D 1275-15 set up-left, modified ASTM D1275-15 silver corrosion test set up-right
ASTM D 1275-15 silver corrosion test, at 150°C | corrosive sulphur | initial | 48 h | 144 h |
---|---|---|---|---|
Standard test set up | DBDS content, mg/kg | 75.7 | 73.7 | 69.9 |
Visual inspection | / | negative | positive | |
EDX wt. % S | / | 0.81 | 2.63 | |
Modified test set up | DBDS content, mg/kg | 75.7 | 60.6 | 36.0 |
Visual inspection | / | positive | positive | |
EDX wt. % S | / | 1.49 | 4.44 |

Figure 5 - Silver strips after standard ASTM D 1275-15 - left and modified ASTM D 1275-15 test – right, at 150°C 48 hours
After 48 hours in modified ASTM D 1275-15 test set up, increased silver sulphide deposition was observed and the oil was tested as corrosive (Figure 5, right). After prolonged testing during 144 h, oil was found to be corrosive in both test conditions. However, silver sulphide deposition, expressed as wt. % of sulphur atoms by EDX measurements, was two times higher in the conditions of continuous air ingress (Table 2).
It can be concluded that modified test with continuous oxygen ingress provided better assessment of the corrosiveness of inhibited oil with DBDS and enabled testing in shorter duration. This test set up is in better correlation to the conditions of oil in free-breathing transformers. Broader testing on different oils in the range of DBDS concentrations is needed to verify the use of the proposed test in silver corrosion assessment.
4. Removal of elemental sulphur from insulating liquids
Mineral oil contaminated with approx. 15 mg/kg of elemental sulphur was successfully treated on lab scale to very low values, bellow 0.50 mg/kg using innovative process based on chemical conversion (Table 3, Figure 6).
Before the treatment, S8 content in the oil, mg/kg | 14.5 |
After the treatment, S8 content in the oil, mg/kg *n.d. - not detected | < 0.07 (n.d.)* |
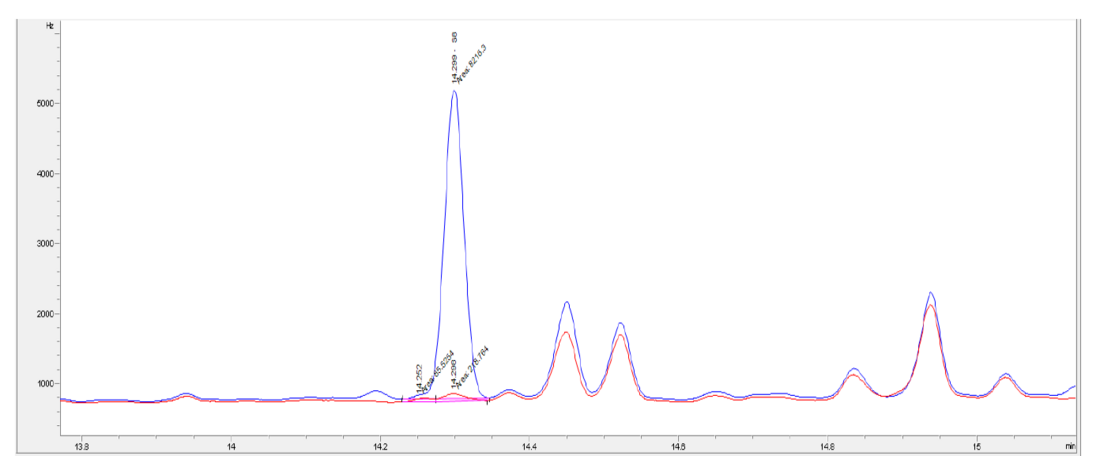
Figure 6 - Chromatogram of S8 before (blue) and after (red) oil lab scale treatment
Further on, large scale treatments were performed after spiking the oil in real power transformer in two different concentrations. Decrease of S8 concentrations was monitored in eight cycles. First treatment was performed on oil contaminated with 10 mg/kg of S8 and second treatment was performed on oil with 20 mg/kg of S8 using same amount of reagent was in both processes. After 8 cycles of treatment, S8 was not detected in first oil treatment; while in oil containing 20 mg/kg it reached 0.54 mg/kg (Table 4.)
Oil cycles | S8 content, mg/kg | S8 content, mg/kg |
---|---|---|
0 (initial after addition) | 14.9 | 20.3 |
1 | 11.8 | 3 |
3 | 2.26 | 3.28 |
5 | 0.61 | 1.78 |
8 | n.d (< 0.07) | 0.54 |
Synthetic ester oil contaminated with elemental sulphur was treated using innovative technology on laboratory scale. Elemental sulphur was completely removed and oil properties were improved (Table 5, Figure 7). The method is applicable for the use in power transformers. Further optimization and testing is needed to verify the technology and find optimal process conditions for the application on real power transformers.
Oil properties | Before the treatment | After the treatment |
---|---|---|
Content of S8, mg/kg | 5.4 | < 0.07 (n.d.)* |
Acid number, mg KOH/g | 0.03 | 0.02 |
Dielectric dissipation factor | 0.037 | 0.019 |
Interfacial tension, mN/m *n.d. - not detected | 36 | 36 |
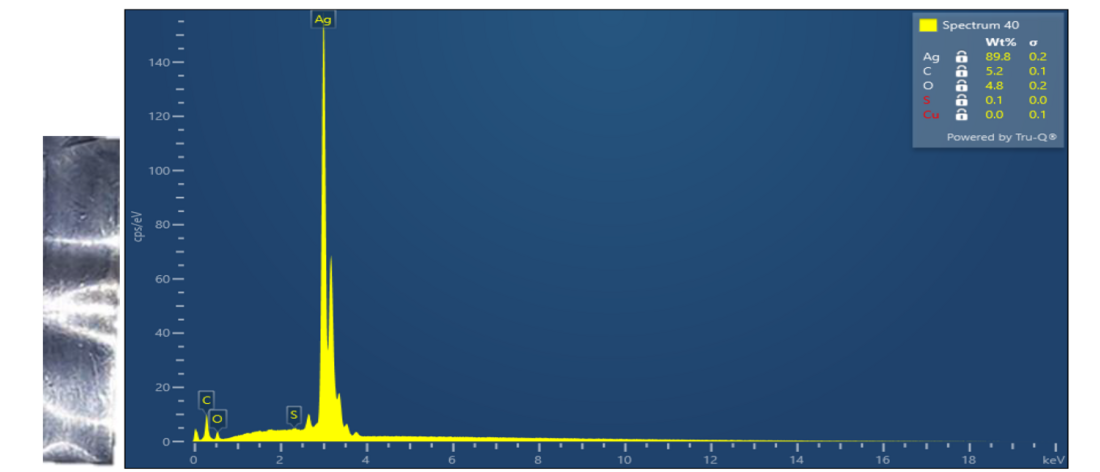
Figure 7 - Silver plate - left and EDX spectrum of silver plate after corrosion test of the synthetic ester oil after treatment - right
5. Conclusion
Silver corrosion problem is becoming more expanded in power grids nowadays. Elemental sulphur was found to be most dangerous sulphur molecule which has high affinity to react with silver. Results of kinetic study indicate that the reaction of elemental sulphur and silver is first order reaction with activation energy of 29 kJ/mol. Obtained results is in good correlation to oil testing practices and service experiences, manifested as easily deposited silver sulphide at lower temperatures. Modified silver corrosion test was found to improve the response of mineral oils containing DBDS towards silver sulphide deposition. Oil which was non-corrosive was tested as corrosive in modified test conditions, which are in better correlation to the free-breathing conditions of particular power transformer. Mitigation of silver corrosion encounters oil treatments to remove corrosive sulphur. Elemental sulphur is difficult to remove and common adsorbents used in oil reclaiming and DBDS removal are usually not efficient in S8 removal. Innovative technology tested on lab scale was found to be efficient in the removal of elemental sulphur from both mineral and synthetic ester insulating liquids and was tested successfully on large scale trial on transformer filled with mineral oil.
Acknowledgement
This research was supported by the Science Fund of the Republic of Serbia, GRANT No. 6700, Development of green technology to mitigate power transformer failures induced by elemental sulphur and change current hazardous practice in transformer oil regeneration – GreenCleanS.
References
- G. Wilson, "National Grid Experiences with Corrosive Sulphur: update mkII, " Euro TechCon, Glasgow November 2012.
- J. Lukic, M. Foata et al, "Sulphur Corrosion Mitigation in Power Transformer Life Extension," presented at the CIGRE Workspot IX, Brazil, 2018.
- M. Foata, K.H. Lindl, M. Da Costa, J. Lukic, J. Jankovic, D. Mihajlovic, "Risk Assessment and Mitigation of Corrosive Sulphur Other Than DBDS," presented at the CIGRE Workspot X, Brazil, 2022.
- J. Lukic, "Silver Corrosion Mitigation - Solutions for Extension of Transformer Life," presented at the TechCon South East Asia, Malaysa, 2017.
- The mechanism of the reaction between silver and sulfur in mineral oil, R. T. Foley, W. Morrill and S. J. Winslow, Transformer and Allied Products Laboratory, Pittsfield Works, General Electric Company, Pittsfield, Massachusetts Received December 22, 1949.
- Kinetics of elemental sulfur reduction by petroleum hydrocarbons and the implications for hydrocarbon thermal chemical alteration, Geoffrey S. Ellis et.al., Geochimica et Cosmochimica Acta, Volume 251, 15 April 2019, Pages 192-216.
- CIGRE Technical Brochure 625, "Copper Sulphide Long-term mitigation and Risk Assessment," 2015.
- M. Dahlund, H. Johansson, U. Lager and G. Wilson, "Understanding the presence of corrosive sulphur in previously non-corrosive oils following regeneration," in Proceedings of the 77th Annual International Conference of Doble Clients Conference, Boston, MA, USA, 26–31 March 2010.
- A.F. Holt, M. Facciotti, P. Amaro, R.C.D. Brown, P.L. Lewin, J.A. Pilgrim, G. Wilson and P. Jarman, "An initial study into silver corrosion in transformers following oil reclamation, " in Proceedings of the 2013 IEEE Electrical Insulation Conference (EIC), Ottawa, Canada, August 29th, 2013; pp. 469–472.
- S. Samarasinghe, H. Ma, D. Martin, and T. Saha, "Investigations of silver sulphide formation on transformer OLTC tap selectors and its influence on oil properties," IEEE Trans. Dielectr. Electr. Insul., vol. 26, no. 6, pp. 1926–1934, Dec. 2019.
- S.Samarasinghe, C. Ekanayake, H. Ma, T. Saha, J. Baniya D.Allan and G.Russel, “A Risk Assessment for Utilities to Prevent Transformer OLTC Failures Caused by Silver Sulphide Corrosion,” IEEE Trans. Power Del., vol. 37, no. 3, pp. 2394-2402, June 2022.
- S.Kamishima, T.Ito and Y.Morishima, “Change in Corrosivity of Insulating Oil Caused by Oxidative Deterioration of the Oil”, IEEE Trans. Dielectr. Electr. Insul., vol. 19, no. 2, p.p. 505-509, April 2012.
- Standard Test Method for Corrosive Sulfur in Electrical Insulating Liquids, ASTM Standard D1275-15, 2015.
- Testing of Insulating Oils – Detection of Corrosive Sulfur, Silver Strip Test, DIN Standard 51353, December 1985.
- Mineral Insulating Oils in Electrical Equipment – Supervision and Maintenance Guidance, IEC Standard 60422.
